Smithsonian x Ecovative: Welcome to the future— building with mushrooms

We Interrupt Your Regularly Scheduled Panel: Future of Food featured Elliot Grant, Danielle Nierenberg, Eben Bayer, Taeryn Kim, and Ashley Mincey at Smithsonian Arts + Industries Building.
If you attend or livestream the Smithsonian's weekly FUTURES events, you'll see the speakers sitting on a stage that we built with mycelium.
The Smithsonian is an historically significant institution, dedicated to the "increase and diffusion of knowledge." Marking their 175th anniversary, and in keeping with that tradition, the FUTURES exhibition showcases innovative concepts, technologies, and designs in transportation, food, home, and other areas. The program is weekly with free admission and livestreams on Thursdays through June 6, bringing together companies, artists, innovators, and other thought leaders together to share their visions of our future — including our CEO at Ecovative, Eben Bayer.

Over 60 M tiles were grown for the Smithsonian stage.
The stage features a repeated, interlocking pattern of soft white 'M's, and a textured, backlit screen projecting the word "FUTURES". These elements and even the support bases of the stage are made of durable-yet-biodegradable mycelium, the 'root structure' of fungi. In fact, the entire stage was designed with compostable materials: wood, MycoComposite™ tiles, and AirMycelium™ foam.
At Ecovative, where I work as an industrial designer, it's wonderful to work with and share the amazing possibilities of mycelium. We were excited to design the stage not just for the interesting engineering challenge, or the chance to build something that wouldn't end up clogging a landfill — it was also a square alignment of values that we share with Smithsonian. In particular, a mission of educating the public about nature and history to inspire a better future. Smithsonian's work encompasses all of the arts and sciences, whereas at Ecovative we are specifically focused on furthering the global use and understanding of mycelium. We want to make sure that mycelium is accessible to all. For example, through our 'Grow It Yourself' kits. We share the belief in education as at the heart of changing the world.

Eri Gentry, George Church, and Steve Wozniak in front of the Mushroom Stage in 2018 at Synbiobeta.
15 years ago, the field of mushroom biocomposites was created by Ecovative. As curiosity bloomed around this new material, it could be found in people's homes as well as in art galleries and scientific exhibitions. Along the way, Ecovative was commissioned for artist installations, set designs, architectural builds such as at MOMA PS1. In fact, this is our second 'mushroom stage'. The first was at Synbiobeta in 2018 — famed geneticist George Church remarked that the backlit mycelium letters “felt velvety soft”.
Setting the Stage
Completed wooden structure for the Smithsonian stage.
As a new material, every project with mycelium amounts to a lot of exploration and experimentation, involving many fellow Ecovators. For this project, our team was prompted to include a large backdrop that could be easily assembled and disassembled in under an hour. My colleague Tyler and I both have woodworking expertise, and chose to build the stage structure out of plywood and 2x4's. For assembly, the backdrop portion is placed flat on the ground, right to left, and screwed together to join as one unit. The backdrop is then tilted upright and slides through the dadoed slot in the right half of the base, following the groove to keep the 8-foot-tall wall upright and stable. Then the left half of the base slides in to cap the backdrop, supported without hardware, just tension and the weight of the base. The front of the base was designed to have a wrap-around bench, so the audience can sit and engage with the stage.
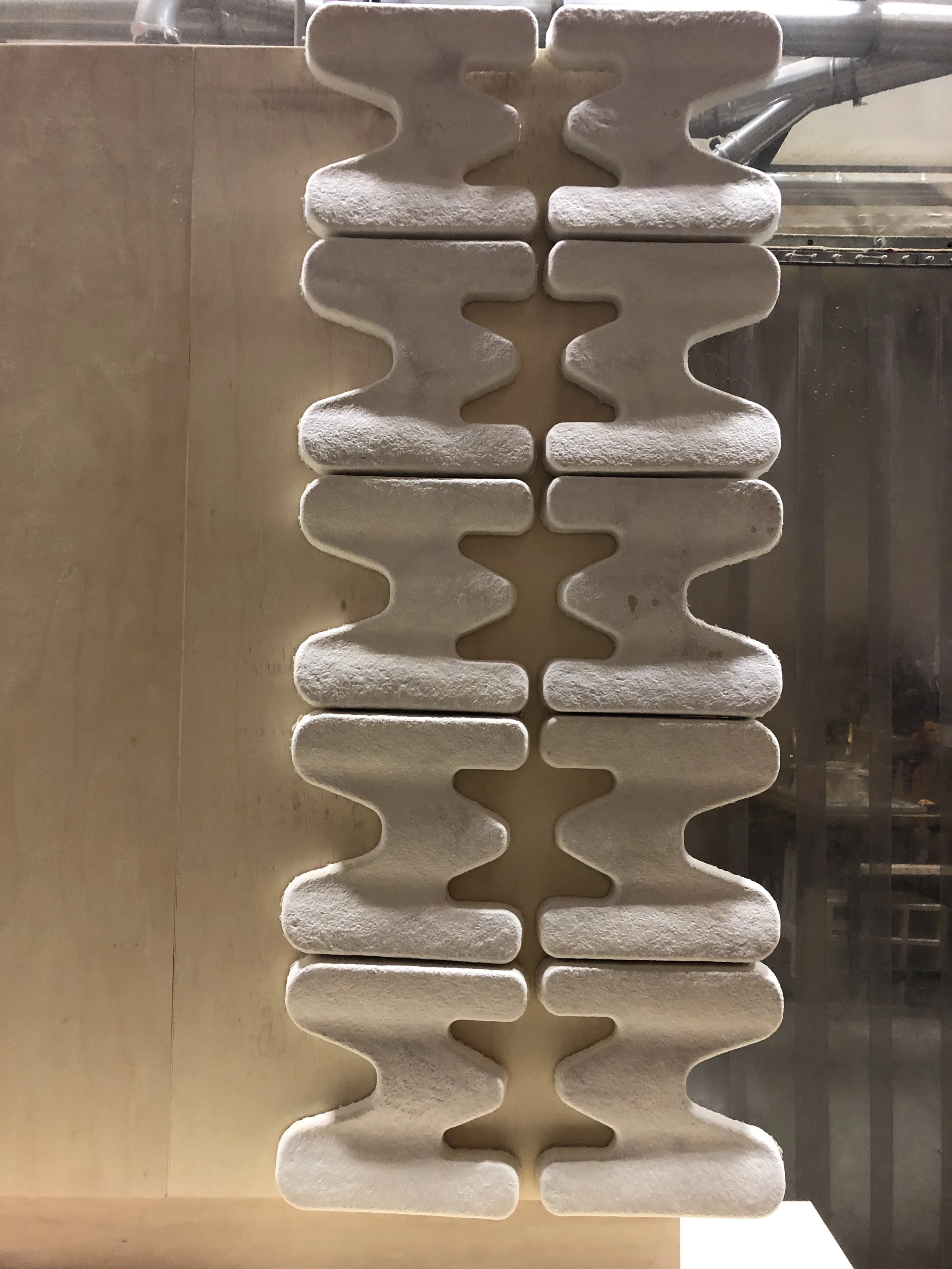
M tile columns alternated to produce a wave of negative space.
We designed a custom set of tiles in the shape of the letter 'M' – for mycelium, mushrooms, MycoComposite, and of course an 'E' for Ecovative if turned sideways. It's also just a nice graphic shape. By alternating and repeating that shape, the tiles create a pattern with negative space. The stage backdrop and tiles are lined with Dual Lock, so the tiles are simply pressed on and gently pried off for removal.
For the lighting, we centered the FUTURES logo, backlit by LEDs and diffused through thin sheets of our mycelium foam, which has its own beautiful natural pattern almost like cheetah print.

LED test on the FUTURES logo lightbox, showcasing Airmycelium’s natural pattern when diffusing light.
Mycelium’s purpose in the project was aligned with its strengths. The MycoComposite tiles are class-A fire resistant, which is necessary for indoor fire codes. The tiles are acoustically absorptive, too, with a high noise reduction coefficient. Our Mushroom® Packaging team CNC'd out the FUTURES logo and grew the 'M' tiles. The tiles are 95% hemp hurd, chipped up like wood, and yet the outside is soft like velvet thanks to the binding mycelium. They flex, but can be broken and composted.
Mycelium materials have a duality to them: they're familiar, yet different. The tiles start wet and end dry. When my colleague Nick announced the newest batch of baker's racks filled with finished 'M' tiles, I couldn't wait to touch them myself the next time I was in the office. I am a designer who has always sought out compostable alternatives and biomaterials for my work. I love using woodshop machinery to process mycelium materials and seeing what happens. Growing mycelium tiles themselves is a patient process, akin to cultivation. It's different from going to the hardware store and buying lumber then starting your design; you’re growing your material inputs to then post-process and use in a finished design.
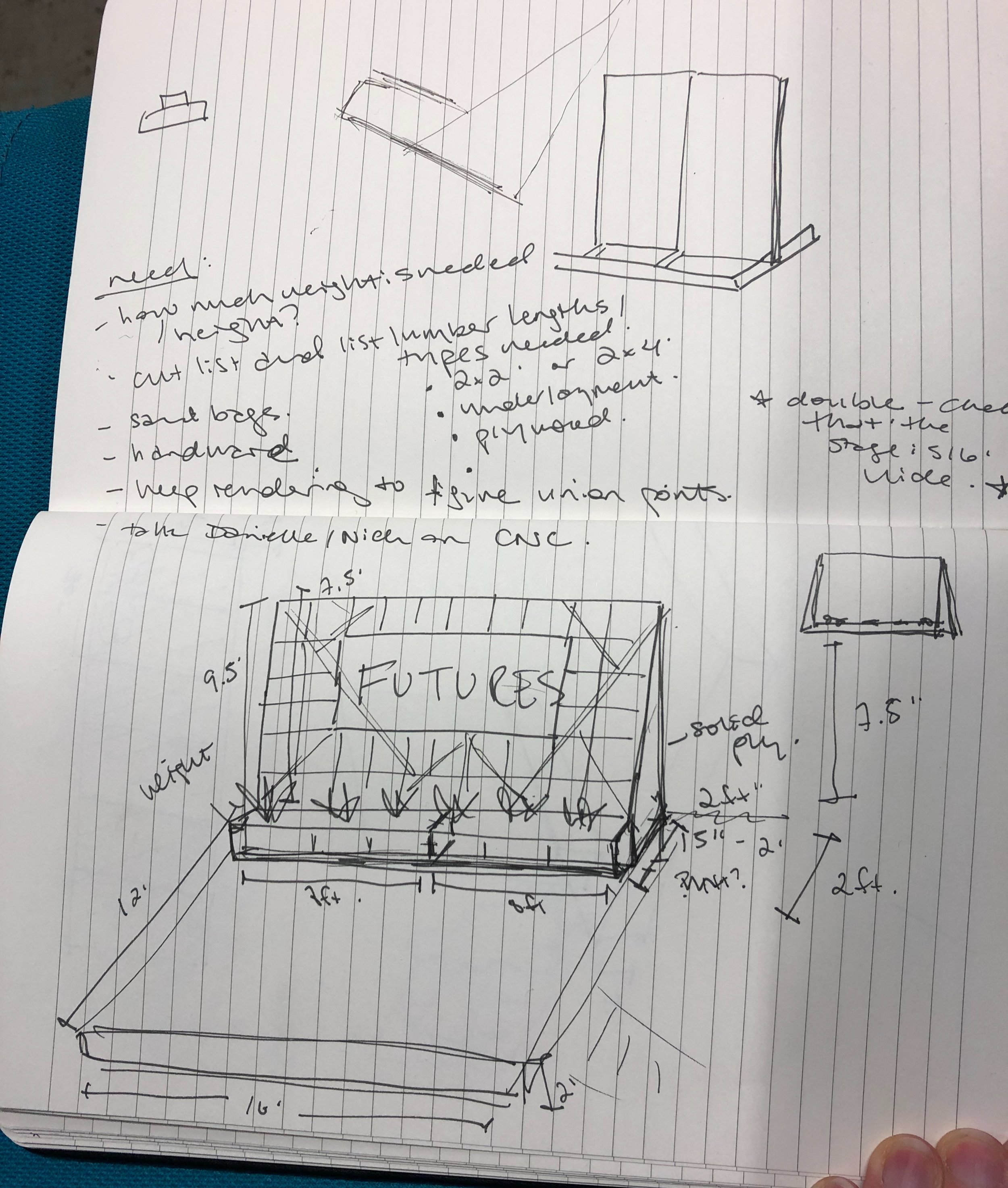
Initial sketch of the stage with rough dimensions

Scale model designed in Rhino and used for generating final dimensions.
There’s a magical moment when the sketches on paper or in the computer give way to physically building something with wood and mycelium. You tell yourself, “it’s happening!” During the final test assembly at Ecovative, to see it all come together was amazing. Many employees peeked in and cheered as we tested the LED colors.
Grace Knight connecting the LEDs of logo lightbox before an event.
No matter how well the design and testing phase went, there is no avoiding the stress of the first event night. I was holding my breath the entire time, hoping nothing went wrong, and thankfully nothing did. By the second event, I knew the space, how to organize the people and install the stage faster, and it all felt more predictable. My relationship with the stage grew and I was confident in how to best set it up, break it down, and make it light up.
Some might ask why build a stage, of all things, out of mycelium? When all of this is possible, maybe the better question than why design a stage with mycelium is, why build a stage with traditional materials? If an event is to host months of discussions about future technologies, why not elevate that conversation using a technology designed for a better future? When the events are over, the stage can be easily disassembled, lighting components and hardware reused, wood recycled, and tiles composted. There isn't the dilemma of planned obsolescence; it can be disposed of without guilt (literally turning into compost), and a replacement can simply be grown. In this sense, the stage makes a humble statement of its own: that even as we look to the future, it is very much possible to build more sustainably today.
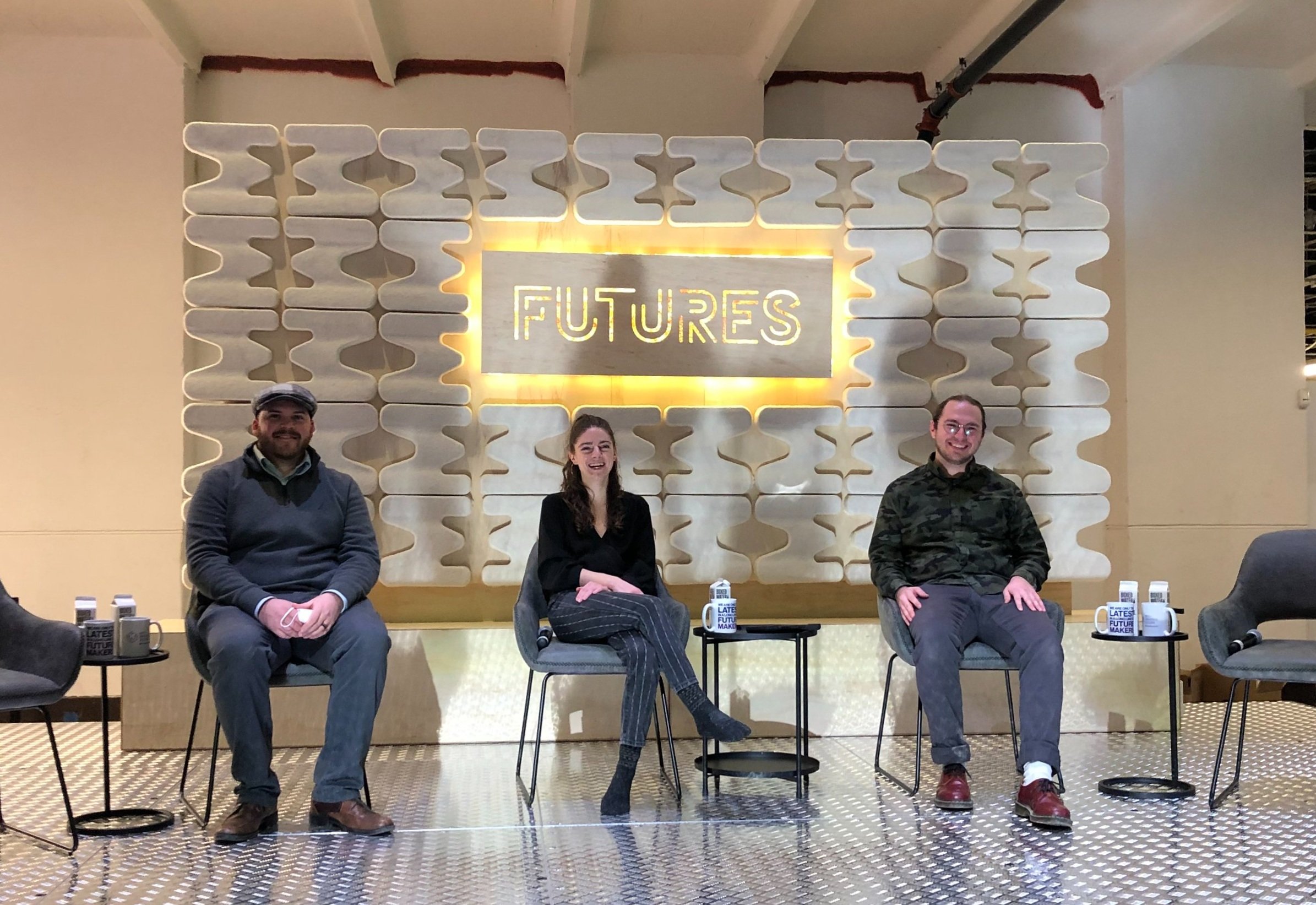
Project partners Tyler Moquin, Grace Knight, and Nick Meyers after a successful installation at Smithsonian for their first event in December.
Want to grow your own stage or something just as cool? 😎 Visit grow.bio to order a mycelium GIY kit to Grow-It-Yourself at home!